Fastest and Easiest Way
to Program Robots
Explore solutions that incorporate advanced vision and motion planning technologies

Step 1
Digitize Workpiece

Step 2
Auto-Generate Toolpaths

Step 3
Deploy Adaptive Motion
Deploy adaptive robot motion with a closed-loop system, correcting part deviations for precise execution.

Step 1
Digitize Workpiece

Step 2
Auto-Generate Toolpaths
Generate optimized robot toolpaths and simulate robot motion before deployment.

Step 3
Deploy Adaptive Motion
Precise and Rapid Set-Up and 3D Reconstruction
Advanced 3D Reconstruction
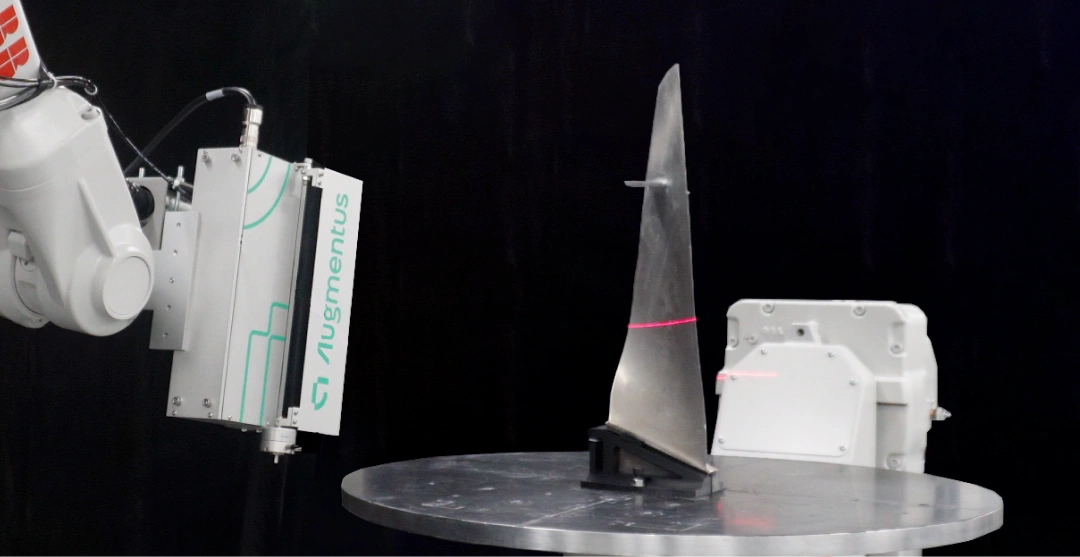
Automated Part Localization
Advanced 3D Reconstruction
Augmentus Vision reconstructs parts with high accuracy, generating a digital twin of the workpiece and eliminating the need for CAD files and manual post-processing.
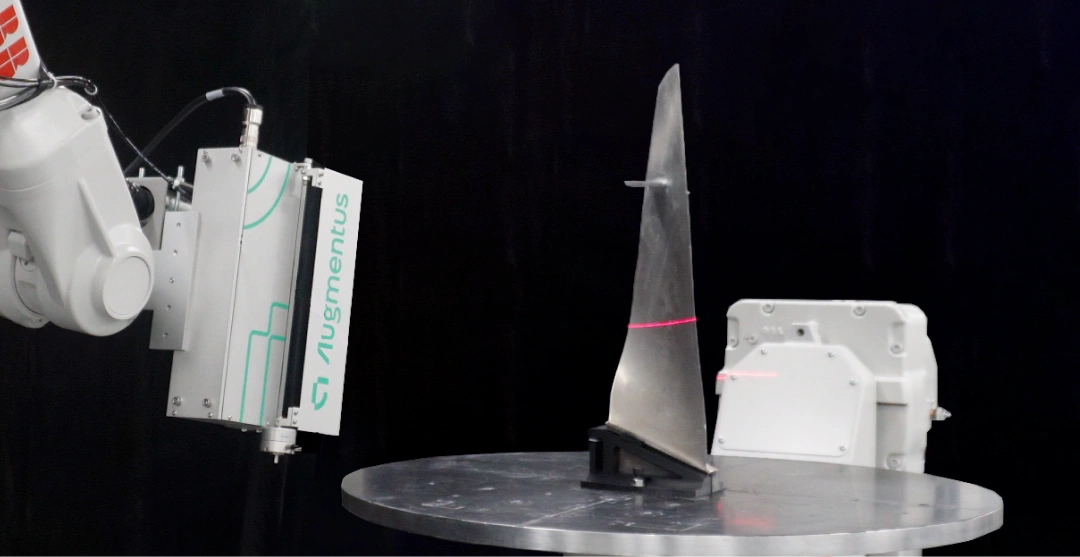
Automated Part Localization
Auto-Generate Complex Toolpaths
Automate toolpath generation for diverse geometries, ensuring precision in robotic processes
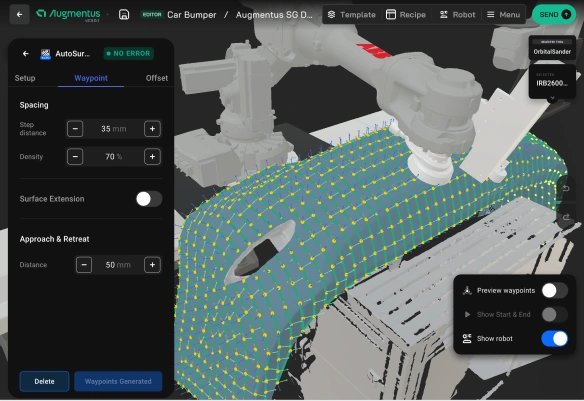
For Complex Shapes
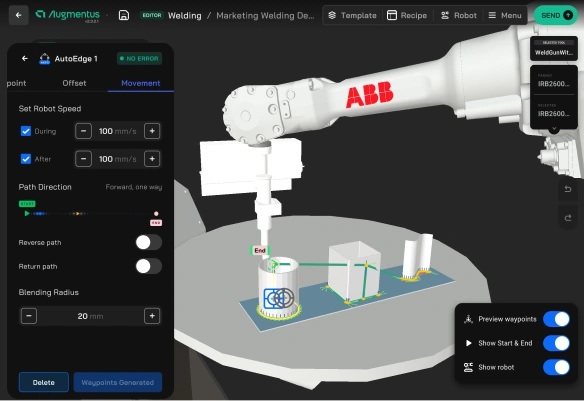
For Challenging Edges
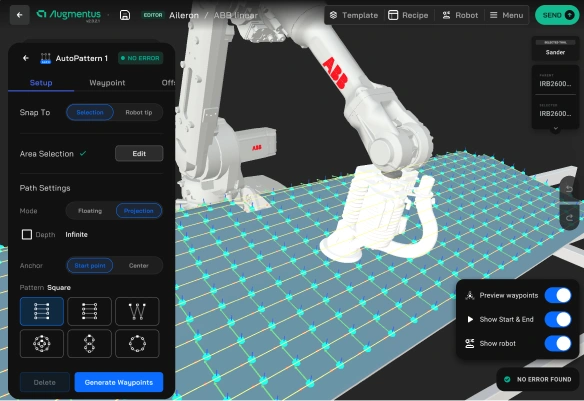
For Predefined Motion Patterns
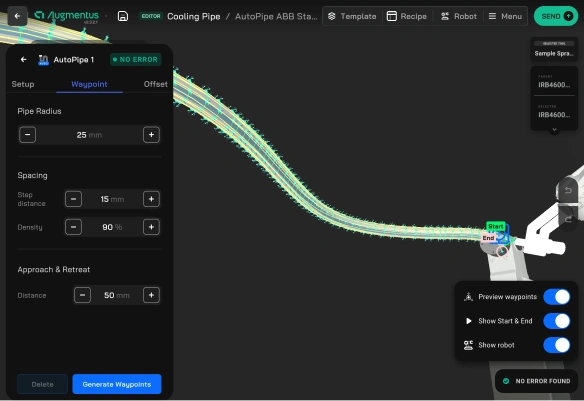
For Cylindrical Objects
Automates path generation for cylindrical or pipe-like objects with precise curvature and alignment.
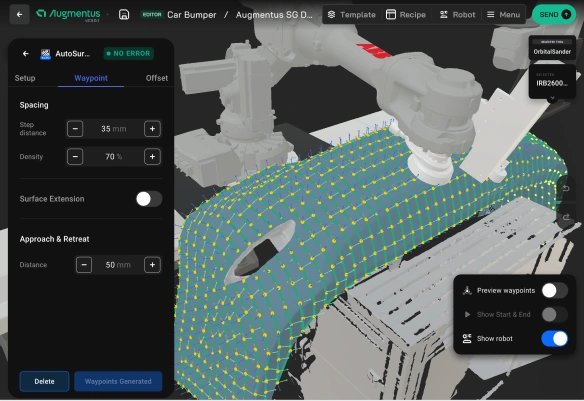
For Complex Shapes
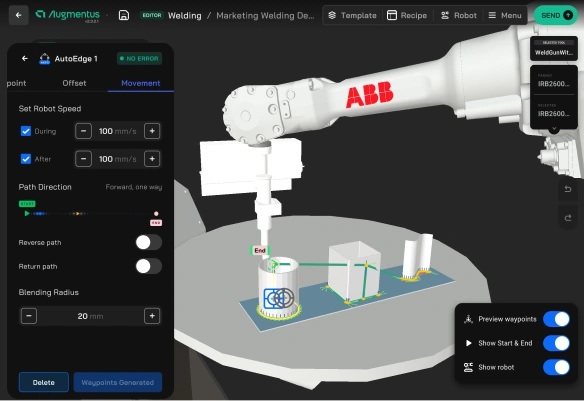
For Challenging Edges
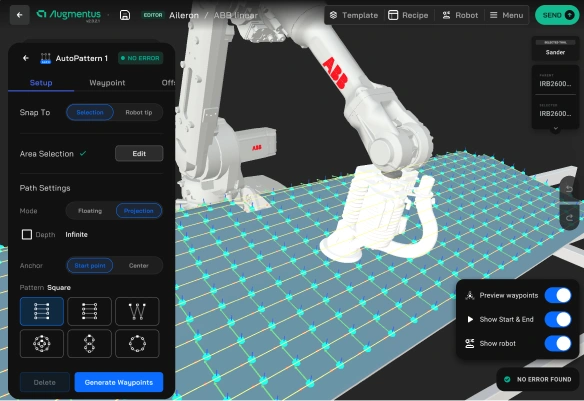
For Predefined Motion Patterns
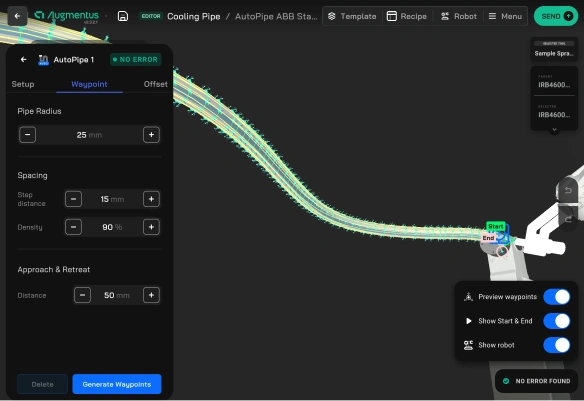
For Cylindrical Objects
Optimize and Simulate Robot Motion
Toolpath Optimization
Offline Simulation
Toolpath Optimization
Offline Simulation
Extended Features

Operator vs Editor Mode
Switch between operation and advanced editing modes.

Template Manager
Save and reuse project templates easily.

Recipe Table
Organize and store process-specific parameters for repeatable tasks.

Custom Tool Integration

Hole Avoidance
Auto-segments holes to ensure accurate motion.

Deploy, Inspect and Correct
Adaptive Robot Motion
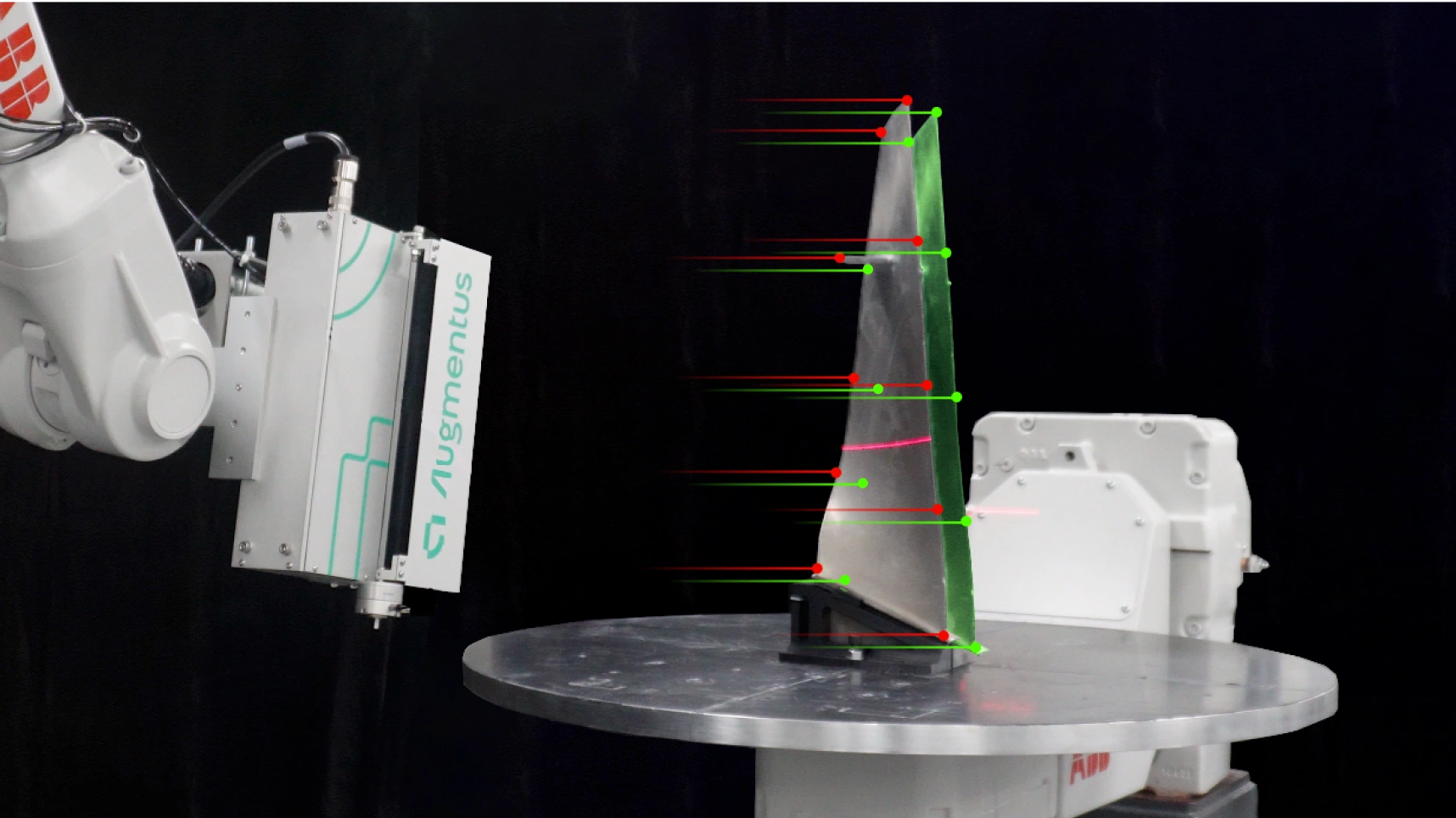
Correct for Part Positional and Rotational Deviation
Augmentus Vision analyzes workpieces to detect positional and rotational deviations, automatically adjusting the robot toolpath to compensate. This capability minimizes the need for precise fixturing while maintaining high accuracy and consistency throughout the process.
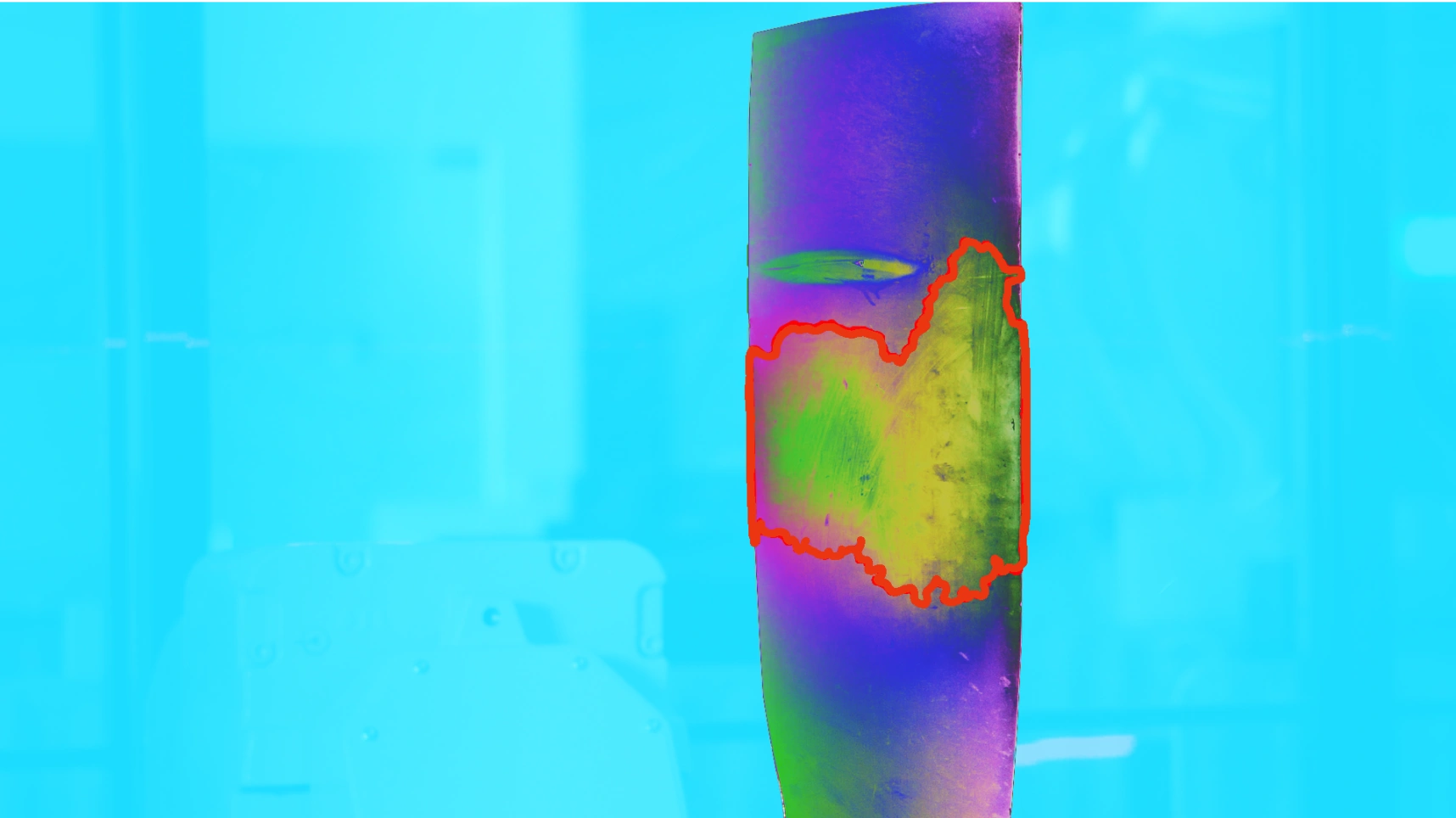
Closed-Loop Inspection to Localized Motion Generation
Flexible
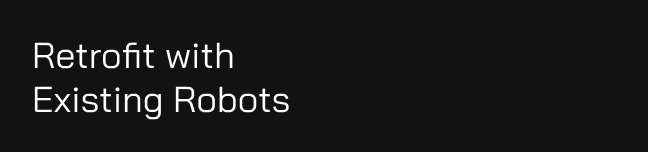

2 Days
Retrofit your robot cell quickly with Augmentus


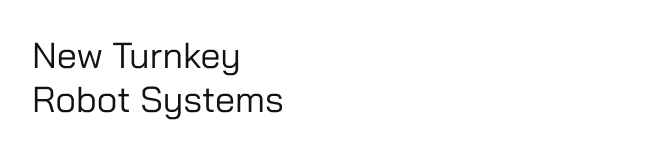


Deep Process Expertise
Tailored deployment with application specialists

Authorized System Integrators Worldwide
Local support through trusted partners
Technical Specifications of Augmentus
Access detailed hardware specifications to ensure compatibility with your automation system setup.
Match Your Needs with the Right Augmentus Solution
Core
AutoPath Software
Pro
AutoPath Software
with Augmentus Vision
Auto
Closed-Loop System
with Adaptive Automation
Core
AutoPath Software
Pro
AutoPath Software
with Augmentus Vision
Auto
Closed-Loop System
with Adaptive Automation
Need Expert Guidance Before Choosing?
Discuss your requirements with our automation experts to find the perfect fit.
Explore Augmentus’ Impact Across Other Applications
For applications where consistent coating thickness and overspray control are essential, even on complex, contoured surfaces.
For applications requiring uniform contact and pressure on uneven surfaces to achieve a smooth, consistent finish without surface damage.
For welding that demands precise torch alignment and controlled speed to produce strong, defect-free welds across various joint types.
For applications where consistent coating thickness and overspray control are essential, even on complex, contoured surfaces.
For welding that demands precise torch alignment and controlled speed to produce strong, defect-free welds across various joint types.